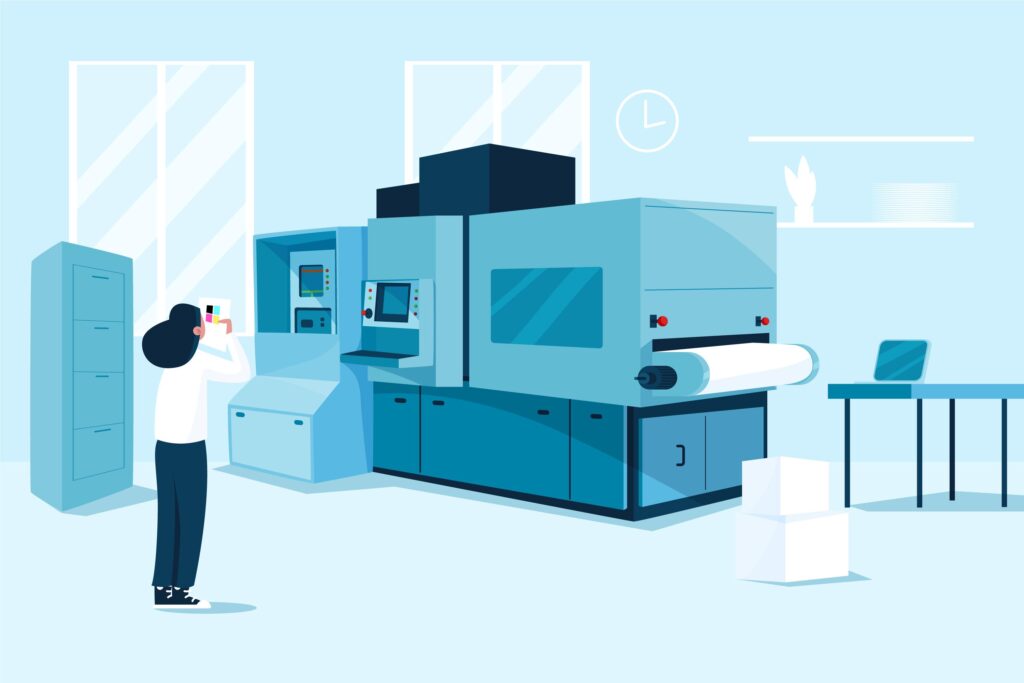
Direct to film (DTF) printing has transformed custom apparel industry to provide impressive colors, detailed reproduction of image and flexibility in multiple types of fabrics. Nevertheless, as any printing technology, the DTF is associated with its own problems that might become headache both to a novice and a skilled printer.
Having to experience poor adhesion, color bleeding, or film peeling errors, these are some of the DTF printing issues that one may possibly tackle, when knowing the solutions of these common DTF printing problems, might save you time, money and endless headaches. It is a very handy guide to the most common problems DTF printers face and ends up with simple, tried-and-tested tips to put your prints back on the rails.
There are accidents where the powder application could go wrong, there are temperature control mishaps and more that we shall be going over to say the least, so that you are fully informed on what you need to do to troubleshoot your DTF printing process to end up with consistently professional results.
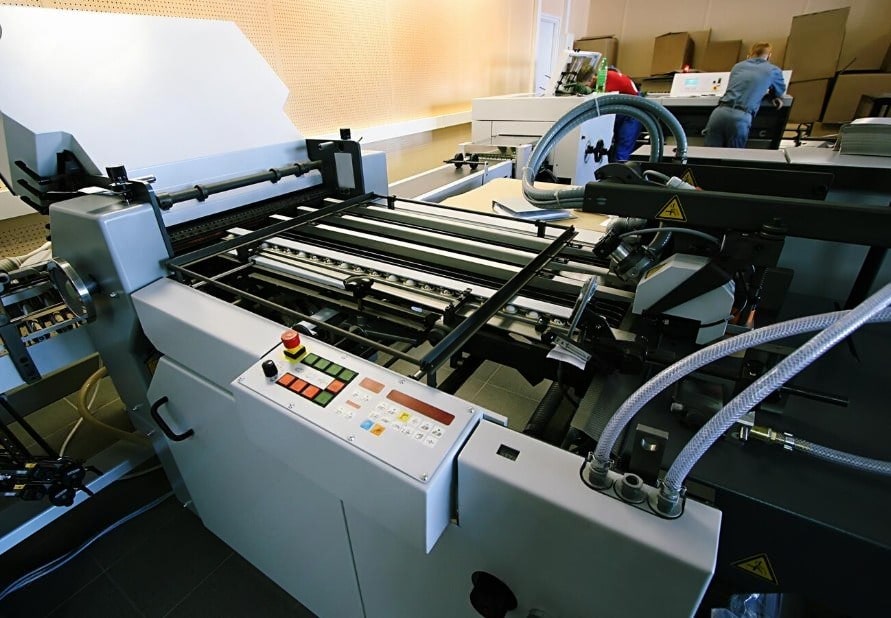
Poor Adhesion to Fabric
To add to the list, one of the most frustrating issues that can arise when doing DTF printing might be when your gorgeous print design not being sticky enough to a garment. Besides bubbles, poor adhesion may appear in a form of lifted edges, full design failure, or patches where transfer did not stick.
Causes of Poor Adhesion
Several factors contribute to adhesion problems in DTF printing. Insufficient heat press temperature ranks among the most common culprits. Each DTF film and powder combination requires specific temperature ranges, typically between 300-320°F (150-160°C). Using temperatures below this range prevents proper bonding between the adhesive powder and fabric fibers.
Poor adhesion also takes places due to lack of sufficient pressure during the heat press treatment. The former has to be high enough so that it makes sure there is total contact between the surface of transfer and the fabric. It should be remembered that most DTF transfers need medium high pressure settings, depending on your heat press specifications.
Fabric pretreatment is an essential factor of success adhesion. Sizing, softeners, etc. that are used on the fabric may form barriers that the bonding can not achieve. Even natural oils transferred in the process of handling can interfere with the adhesion process.
Solutions for Better Adhesion
Begin by ensuring that your heat press parameters are suitable to your needs of both DTF film and powder. To verify the real platen temperature, use a quality thermometer because the heat press displays can be used inaccurately. Coarse the settings of pressures to allow even contact over the whole design area.
Wash out when available with pre-wash fabrics sizing and any chemical processing. In the case of un-pre-washable garments, a printing field should be clean by means of a lint-free cloth and isopropyl alcohol.
When you are changing your process, consider the fabric type. Somewhat different settings are usually required by the synthetic fabrics as compared to the natural fiber setting. Cotton blends may be more time consuming as dwell times or require minimal increases in temperature to achieve optimum adhesion.
Cracking and Peeling After Washing
Designs that crack, peel off or fade away after the initial wash are nothing to build my confidence on DTF printing. The frequent source of this common problem is mechanical failure of curing or improper circumstances in cleaning.
Understanding Curing Requirements
Proper curing does not just end with the first application of heat press. The adhesive powder requires enough temperature and time so that it cross links thoroughly and bonds to the film and fabric. Poor initial curing exposes the design to wash related mechanical stress.
The curing process persists when the transfer has been carried out of the heat press. Transfer to cool occurs prior to manipulation, which will cause premature stress to the bonds which are still forming.
Preventing Wash-Related Damage
In case of wash durability problems, increase your heat press dwelling time by 5-10sec. Longer-term durability can be enhanced by higher temperatures in the recommended range as well, though never by going above manufacturer specifications.
Inform consumers on how to take care of them. It is advised that it should be washed with cold water and by using weak detergents as well as avoiding the use of fabric softeners which may after a period of time degrade the bond between the adhesives. Before washing turn garments inside out to minimize friction on the printed area.
A secondary curing step in critical usage is to be considered. There may be some DTP printers, which transfer some extra heat after the primary change in order to guarantee full adhesive softening.
Color Bleeding and Ink Migration
The problem of color bleeding happens when inks go past what they have been supposed to be, that is, they cause fuzzy edges and mixed colours or general degradation of the design. This issue of DTF printing can spoil all the well-planned designs.
Ink-Related Causes
Overload of ink is also classified at the top of the list of causes of color bleeding in DTF printing. When the ink profiles provide an excess of ink to the film then the extra ink may migrate laterally, particularly in fine details, or high-coverage domains.
Bleeding may also be as a result of incompatible ink and film combinations. The other DTF films possess different ink absorption speeds and surface properties which would influence the behavior of inks during the printing process and curing.
Controlling Color Bleeding
Take a look at your print traces, and cut the ink limitations, in the event of any bleeding. The majority of DTF applications work well at a overall ink coverage in the range of 240-280%, depending upon the combination of specific ink system and film.
Make an optimized preparation of ink by changing your RIP software settings. This can be achieved by linearization and color profiling to make color reproduction accurate without over-deposition of ink.
Keep check on the temperature and humidity of your printing environment. The presence of a lot of humidity may delay the inks drying time aiding the chances of bleeding in the course of the printing process.
Powder Application Issues
The stage of applying adhesive powder has numerous openings where issues may arise hence getting into the final transfer quality. There are uneven concentration of powder, too much or too little coverage which affects final outcome.
Common Powder Problems
The situation of uneven distribution of the powder forms spots of good and poor adhesion in one and the same drawing. This is normally because the shaking when the cosmetic is being applied was not adequate or the powder was dry but had been clumped together because it had been exposed to moisture.
Excessive use of the powder might result in a number of problems which are associated with thicker transfer, decreased malleability, and even colour change. An excess amount of powder may also pollute your curing equipment.
Optimizing Powder Application
Find a regular technique of applying the powder. Powder should be applied right after printing when the inks are still damp. Shake in fine, even up-down motions so as not to leave any area uncovered yet forming thick clump of powder.
Blot off, but with care, unlocked powder. The rest of the actual excess can be removed after a soft brush redistributes the powder concentrated into heavy application areas to the less dense zones of coverage.
In order to avoid oil dispersion and clumping eliminate moisture by keeping store adhesive powder in sealed container with desiccants. Discard any powder which is clumpy or becomes less flowable.
Film Tearing During Transfer
A transfer process can damage a print job by tearing the print in part or in whole and ruin the film. This issue is frequent at the step of peeling when the carrier film is removed after the printing of the design.
Causes of Film Tearing
The wrong processing temperatures and time of peeling are the main reasons of film tearing. Stretching and buying could occur when you peel too soon before the film has cooled. On the other hand, longer waiting increases brittleness such that, the film is likely to break.
The excessive pressure of heat press may fix the film to the fabric textures and it becomes very tough to remove the film without continuous tearing. This is an especially big problem with textured or heavyweight cloths.
Proper Film Removal Technique
Before peeling, adhere to the recommendations of the manufacturer. The majority of the DTF films ought to be taken off at warmer but not hot. The movie ought to be hot to the touch yet not hard to handle. During the peeling process, a gradual push should be applied as opposed to jerking. The best thing to do is start with one corner and keep the angle low as you continue to get straight as you pull across the design.
Change the pressure of the heat press according to fabrics. Fabrics that are textured can also demand lesser pressure so as not to have too much film embedded in the fabrics but still getting the right adhesion.
Temperature Control Challenges
Consistency of temperature control during DTF printing operation has various quality implications. Change in temperature may affect the drying time of ink, adhesion of powder and quality of the final transfer.
Environmental Temperature Effects
The printing stage and the curing stage of DTF production are susceptible to room temperature and humidity. There is a risk of ink drying slowness on high humidity and of powder flowability and they might influence the consistency of curve.
Heat presses will have variability in temperature (unit to unit) and drift with time. Frequent calibration will make sure your adjustments are compatible with the real temperatures felt by the transfers.
Maintaining Temperature Consistency
Test heat press temperatures with a separate infrared thermometer at a usual increment. Readings at several locations along the platen should be compared to determine hot or cold spots that may interfere with the quality of cure.
Think of environmental controls on your printing area particularly when there are high humidity or much temperature fluctuation. Stable environment enhances reliability of the process.
Monitor the curing oven temperature should one use secondary curing processes. Internal temperature stability in the curing chamber impacts on the ultimate adhesive characteristics and bond strength.
Design Size and Placement Problems
When DTF printing is concerned, proper size and placement of design issues largely determine the outcome. Designs that are too big to transfer adequately, design that is misplaced and so as a result the press coverage is interfered with or even the scaling issue interfering the quality of the image are all common problems.
Sizing Considerations
Big designs need better control of temperature and pressure in order to achieve even drying to the whole surface. Limitations of heat press because a bulky design might not be covered adequately resulting in a few spots of not being cured as well as bonded.
Minute designs that have really small details might not transfer because of minimal lines widths of the DTF process. Print under some size can be illegible or not transfer at all.
Optimizing Design Parameters
Design with your limits of the capacity of the heat presses but leave plenty of margin to allow proper distribution of the pressure. If the designs are near your press size limits you may wish to cut it into several parts and apply them separately.
Set Minimum line widths and text sizes depending on your capabilities of the DTF system you are using. Try different scales to find workable boundaries to your plant and your process variables.
Before establishing the design position, think about the structure of the garments. There are various features of the garment that include joints, pockets, and such like which interrupt the contact of the heat press and alter the quality of transfer.
Ink System and Maintenance Issues
The maintenance of DTF printers has a direct effect on quality and reliability of prints. Lack of maintenance causes a number of printing issues that can be confused with the problems of the processes, though they are the problems of the equipment.
Common Maintenance-Related Problems
Plugged print heads cause yanks in printed designs making colors to be missing, banded, or have full drop off. This issue tends to be cumulative and slowly developing such that it can be noticed only when the quality of prints is severely impaired.
The problems of working with contaminated ink systems are shifts in color, a decrease in color saturation, or variability of the ink flow. An even bigger problem that arises is the cross-contamination between colors which is rather problematic in color accuracy.
Preventive Maintenance Strategies
Set up regular cleaning procedures according to the amount of printing and the suggestion of your manufacturer. Nozzle inspections done every day enable early detection of arising issues before they become grave.
Apply relevant solutions and practices with regards to your particular printer model. Do not use any incompatible chemicals that could destroy the seals or other component of the system.
Keep track of ink levels and duties should not wait until the cartridges are completely dry. Drying of cartridges may cause the introduction of air into ink system resulting in ink flow issues and may result in damage to the head.
Quality Control and Testing
Meaningful maintenance of systematic quality control processes can detect DTF printing issues before they become costly to production runs or in customer orders. Frequent test and records build a platform of standardised results.
Establishing Test Procedures
Make up standardized test prints that measure every facet of your DTF system. The color patches, the small detail areas, the solid coverage areas, the text of different sizes should be included to give a complete analysis of the performance of the systems.
Make other prints successfully and save document process parameters (these can serve as the foundation settings of previous fabric types and design properties). This recording then proves immensely helpful in case of problem solving, and training.
Monitoring and Adjustment
Monitor the quality progress measurements to recognize the trends, which may be the beginning of the mounting issues. A slow variation in adhesion, color accuracy or any other parameter may represent an indication of maintenance or a drift process.
Put in place correction procedures of the common issues to allow fast resolutions without the need to go through a lot of troubleshooting. Write down the effective solutions and refer to them in future and in training personnel.
Troubleshooting Systematic Approaches
Once there is DTF printing problem, troubleshooting methodology can be applied in order to conclude the issue faster and be able to avoid recurring issues. The random solutions usually create the feeling that problems are being solved without solving the problems.
Isolation Techniques
One variable should be changed at a time during the trouble shooting period so as to isolate the main cause of the problems. There are various changes occurring at the same time; hence it is not easy to tell which modification addressed the problem.
Where possible test known-good materials so as to isolate variables. By taking advantage of past successful combinations of ink, film and powder, the parameter of problem isolation may be simplified to material or process parameter.
Documentation and Learning
Build institutional knowledge by recording the symptoms of the problem, tried solutions, and ultimate solutions. Such recordings are especially useful whenever used to train new employees or in case of related problems in the future.
Respond in the forums and user groups with best solutions to other DTF printers when possible. The printing community of DTF can quite frequently offer excellent points of view and different ways of resolving issues.
Achieving DTF Printing Success
To be a master of DTF printing, it is important to know these common mistakes and their fixes, yet all that finally matters is to apply good techniques and maintain the system on a regular basis. The point is that the systematic approaches to the production and troubleshooting should be developed in such a way that they guarantee us the high-quality and repeatable results.
Note that the DTF printing is a constantly developing technology, and new materials, inks, and methods appear periodically. Keep yourself informed of new developments in manufacturers and local knowledge to take advantage of the enhancement in the sector.
The most important thing is to document the things that you succeed in, and keep better records of solutions that are effective in your unique setting. Such knowledge is very valuable when you increase your abilities in DTF printing and work on more complicated projects.
With such typical DTF printing issues dealt with ahead of time and the recommended remedies carried out, you will be in an ideal position to deliver quality professional print consistently, at the level that meets the quality expectations and of your customers.