How to Choose the Right Heat Transfer Roller Machine – Expert Guide
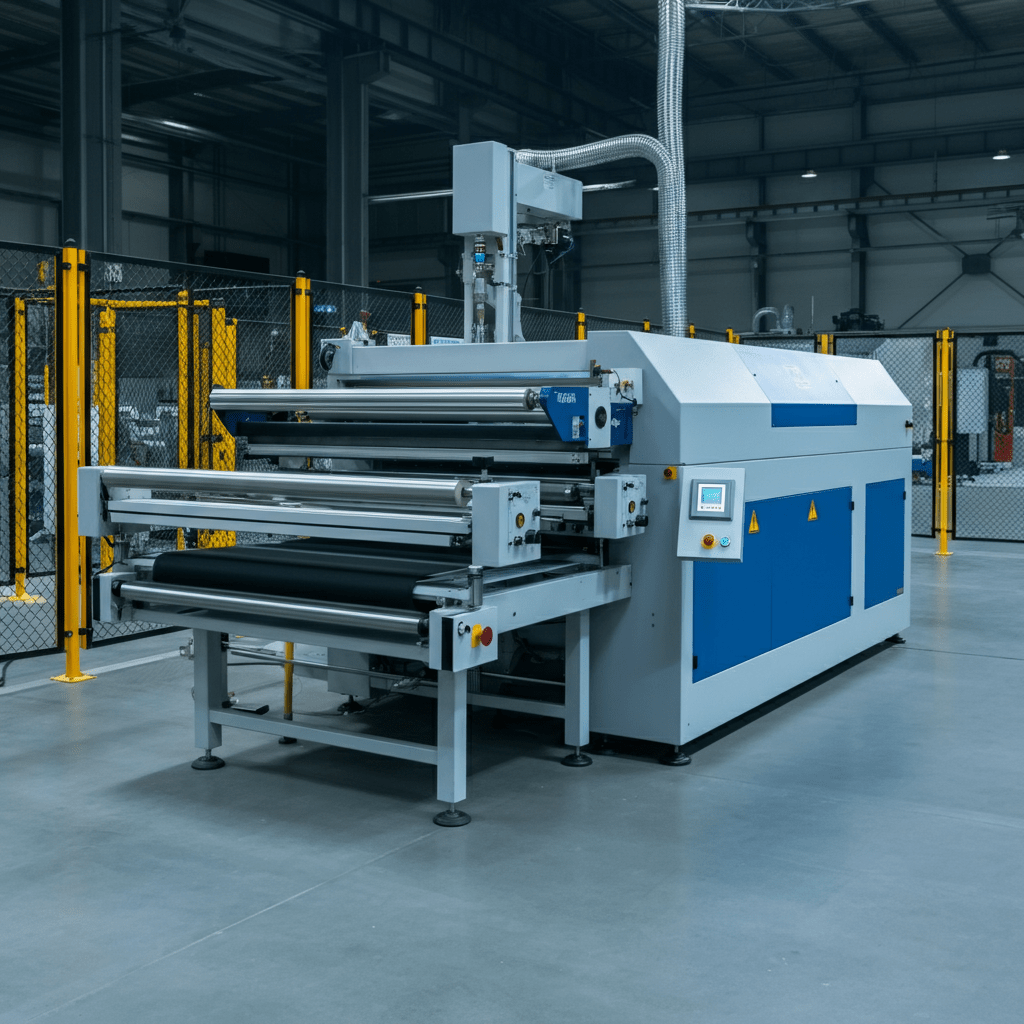
The right choice of the heat transfer roller machine may determine the success or failure of your printing business. Manufacturers usually face problems locating the equipment that supplies them with quality that is consistent and at the same time being cost-effective since the market is flooded with many options. Using the wrong option may end up wasting materials, customer frustration, and huge monetary losses.
This thorough guide will take you through all the facts there is to know about selecting the right heat transfer roller machine that best suits your exacting requirement. You will know about the various types of machines and be in a position to make an informed choice of the machine investment that you need to take that can enable your business to grow.
You may be a startup in search of your first machine or a more mature company that is expanding your capability; one way or the other, this professional guide will assist you as you wade through the complex maze of heat transfer equipment with confidence.
Understanding Heat Transfer Roller Machines
Heat transfer roller machines are special purpose machines created to melt heat activated vinyl, sublimation transfers, and other items that have a melting heat-sensitive content to diverse substrates. In comparison to conventional heat presses, which require flat plates, roller machines are equipped with cylinders which are heated and are in motion and hence can be used on mass production runs.
The way these machines function is by inserting a material into heated rollers which apply a constant heating and pressure to all areas in contact with it. This will allow even adhesion and doing away with uneven pressure distribution which is typical of conventional flat-bed presses.
The greatest benefit of Roller machines is that they have the capacity of supporting a lot of products at a given time. They are able to print such things as t-shirts and banners, vinyl decals and promotional materials with impressive speed and precision.
Types of Heat Transfer Roller Machines
Cold Peel Roller Machines
Cold peel roller machines are designed for transfers that require cooling before the carrier material can be removed. These machines typically operate at temperatures between 300-350°F and feature extended cooling zones that allow the transfer to set properly before peeling.
The cold peel process produces high durability and wash resistance therefore such machines are suitable to use on apparel and items that require excessive washing. The time to process is more as a result of which there is a better stick and there is no likelihood of transfer failure.
Hot Peel Roller Machines
Hot peel machine is used to remove the carrier material instant; the transfer is still warm. They work at close temperatures to those of cold peel machines, but the processing paths are shorter and they alleviate peeling instantaneously.
These types of machines are best suited in high rate manufacturing industries where fast turnaround is the key. The hot peel process prefers special transfer materials that release quickly and so compatibility of materials is an important factor.
Dual-Purpose Machines
New dual use roller machines re introduced the versatility of supporting both cold and hot peel transfer, by way of adjustable cooling zones, and variable speed control. They are multi talent machines whose prices are high yet give optimum flexibility to various production requirements.
This capability of interchanging functions makes dual purpose machines appealing to enterprises engaged in many lines of products or businesses which do not wish to acquire or extend their operations through purchase of new equipment.
Key Specifications to Consider
Roller Width and Diameter
The width of the roller sets limits on the largest size materials that can be handled. Popular widths are 15 inches in small-scale job and 64 inches large-format usage. Choose the roller width considering the average size of your products to create the possibility of growth.
Diameter of rollers has a bearing on the heat distribution as well as pressure application. Larger diameter rollers distribute that heat more uniformly to a longer contact time, which means better quality transfer. They however occupy more space and take more energy.
Temperature Range and Control
The direct relationship with temperature control accuracy and quality and consistency of transfer is given. Machines providing temperature capability of 250-400 o F should be sought with accuracy of greater than or equal to +/- 5 o F. Sophisticated machines have several temperature levels, which create the most efficient heat diffusions.
Programmable digital temperature controllers enable the operator to store the settings according to particular material and transfer. This characteristic saves time during installation, and it also allows the same results within consecutive production.
Speed and Throughput
The speed of production can normally vary between 3-15 feet per minute depending on the material needs and machine fabrication. When moving faster the productivity can be augmented at the expense of the quality of transfer in case the speed is inadequately adjusted.
Think about the quantity of production and find equilibrium between speed requirements and quality ones. The controls can be set to preset variable speeds that are adaptable to adjust settings on various types of materials and transfer forms.
Pressure Adjustment
Uniform transfer adhesion is guaranteed by consistent application of pressure on the surface. Seek those machines that have adjustable pressure and pneumatic or hydraulic apparatus facilitating continuous pressure during the procedure.
The widespread of pressure increases in importance as the rollers get wider and transfers bigger. Sophisticated machines have pressure monitors which tell the operator when changes occur that may interfere with quality.
Material Compatibility and Versatility
Substrate Compatibility
Various roll machines perform well only with certain type of substrates. Think about the types of materials that you are going to mostly process, such as weight, thickness and composition of such fabrics. There are those machines that accommodate all types of materials; be it lightweight polyester, heavy cotton blends and others and some that accommodate specific types of materials.
The man made materials will sometimes need to be at a different temperature and pressure compared to the natural fibers. Because the substrates which may be processed should be variable, your selected machine must be able to work with the entire gamut.
Transfer Material Options
The kind of transfer materials you are using would go a long way in determining the kind of machines you use. There are certain processing requirements to heat transfer vinyl (HTV), sublimation transfers, plastisol transfers and digital transfers.
Look at the adhesives, release and peel of your favorites. Certain machines have been very good with certain types of transfers and handicapped with other types.
Thickness Capacity
The capacity of the maximum thickness fixes the number of products you can handle. Standard machines usually can accept materials not thicker than 0.5 inches, whereas the heavy-duty ones will handle even more material such as hoodies or padded clothing.
Not only should the thickness of the base material be taken into consideration but anything added to it due to seaming, pockets, or decorations that may alter the thickness of the base material throughout the processing process.
Production Volume Requirements
Small-Scale Operations
In cases where less than 100 items are processed daily, smaller machines with width of 15-20 inches tend to have adequate capacity hence the use of compact roller machine. These machines also have low first-cost, lesser levels of energy consumption and they provide professional results.
Machinery that have fast setup capacities and which have simple control settings can be an advantage even to small-scale operations where training of operators is minimised and hence errors with respect to control of the machine.
Medium-Volume Production
The 30-44 inch machine width with a better durability feature is good in operations that process 100-500 items per day. These machines are space and energy efficient, having the right capacity of production.
The intermediate volume of operations is characterized by programmable controls and automatic features that minimize the labor expenses, as well as yield consistent quality with a larger production run.
High-Volume Industrial Applications
High-volume processing (more than 500 items) daily implies industrial (44-64 inch wide) and industrial strength, with a construction that is able to work around the clock. These machines have well-developed monitor systems and automation.
The volume requires machines with little downtimes, easy access to maintenance, and a large capacity to produce a consistent quality of thousands of products in a day.
Budget Considerations and ROI
Initial Investment
Simple heat transfer roller machines will cost you between 3,000 to more than 50,000 dollars depending on the size of the model you want to invest in. Include cost of installation, cost of training and alterations to a facility when determining total investment.
Pay attention to some leasing possibilities on expensive machines, in particular, when it is a cash-flow issue. With leasing, it is possible to enhance access to better quality equipments and still hold the working capital to be used elsewhere in the business.
Operating Costs
Continuous costs would be electric cost, maintenance, replacement parts and operator training. Machines which are energy efficient might lead to high costs at the very beginning but offers a lot of economic savings in the long run with lower utility expenses.
Include the cost of consumable costs such as transfer supplies, cleaning materials and replacement green rollers in the total operating costs. Machines may also need proprietary consumables which have an effect on long-term profitability.
Return on Investment
Compute the possible additional revenue that may be earned due to enhanced production capacity, low labor cost, and enhanced range of service. A lot of companies find the ROI in 12-18 months operating the right mix of machine capabilities to the demands in the market.
To consider ROI, consider value added to improved consistency and reduced waste. Better machines can sometimes be paid off by causing less waste of materials and fewer complaints of customers.
Safety Features and Compliance
Operator Safety Systems
Contemporary roller machines have various precautionary measures such as inbuilt emergency stop, safety or guards, and auto-stop mechanisms. The features ensure the safety of operators against burns, crushing, and other risks applicable to heated rotating machinery.
Choose those machines that have access to emergency controls as well as distinguishable safety indicators. Quality safety training minimizes accident occurrence and makes employees adhere to safety regulations at workplaces.
Ventilation Requirements
When there is a tendency of heat transfer processes there are chances of fumes being generated and proper ventilation is necessary to sustain good quality of air. Certain machines have ventilation systems mounted on them and others have no systems whatsoever to ventilate so an exhaust system has to be mounted.
When comparing machines, take into consideration cost of ventilation and facility demands. Adequate ventilation helps safeguard the health of the operator, and may also be a requirement by the local authorities.
Electrical and Fire Safety
Check that selected machines are within local electrical and fire solutions. Also, UL listing or other similar credentials visibly indicate that such a product meets the safety requirement and insurance coverage might require it.
Review the electric needs and make sure such needs fit within your establishments current capacity without overloading. There are certain machines which use special electrical connection or three-phase power.
Maintenance and Support
Routine Maintenance Requirements
Proper maintenance is able to prolong the life cycle of the machine and also maintain constant operations. Learn maintenance schedule, procedures, and their costs that are required to maintain your machine in the best condition.
Then there are machines which must be cleaned and lubricated after each working day or once every week or per month. Consider the factor maintenance time in your production schedule and operators should be well-trained.
Technical Support and Service
Such technical support would be essential when technical issues occur to the equipment. Compare support options, response times and the availability of support in your locality offered by manufacturers.
Choose equipment of a manufacturer who has a good service network and parts. Long-term guarantees may give relief of mind and that of a secured investment.
Replacement Parts Availability
Have critical replacement parts available and at a reasonable cost. Some of the manufacturers have a good inventory of parts, others could also have a long lead time on special products.
Choose to store emergency spare parts in order to reduce downtime. Typical items that can be replaced due to usual wear are rollers, heating elements and controls.
Making Your Final Decision
Evaluating Demonstrations
Get the potential suppliers to demonstrate the machines with your precise materials and uses. This practical assessment highlights the behavior of the performance which is impossible to understand with specifications only.
To the demonstrations bring samples of your regular products and transfers. This will enable you to test the effectiveness with which the machines address your applications and also detect any problem.
Comparing Warranties and Service Agreements
Machine warranties by both manufacturers and models are very different. Compare the terms of warranty, limit of coverage and the service agreement options before coming to your ultimate decision.
Long term warranties and service contracts are the second type of insurance against surprise repair costs, however this comes at an added expense. Account these options according to your risk tolerance and budget limitations.
Planning for Future Growth
Choose machines that will support the organization in its phase of growth as the organization continues to meet the needs of the market. The initial purchase can be a little bit bigger than needs to pay more initially but have flexibility to expand with no need to purchase other equipment in future.
Think of modular machines which can be upgraded and expanded as your company develops. The strategy can offer an economical way of getting more capacity without jeopardizing your initial investment.
Maximizing Your Investment Success
Selecting a proper heat transfer roller machine is always important to take into account your particular requirements, production needs and long-terms business objectives. The selection guide of the correct heat transfer roller machine is all about toggling the issues of performance, capacity, and costs peculiar to your operation.
Effectiveness of heat transfer roller machines is beyond the making of the initial purchase decision. Consistent operator training, maintenance, and support contacts lead to adequate care of your investment leading to maximum value in the life of the product.
Give yourself ample time to research and adequately test your possible choices, ask to see demonstrations, and talk to other users. The suitable machine will become a pillar to build business development and customer satisfaction even in future years.