Emerging Technologies in Digital Textile Printing
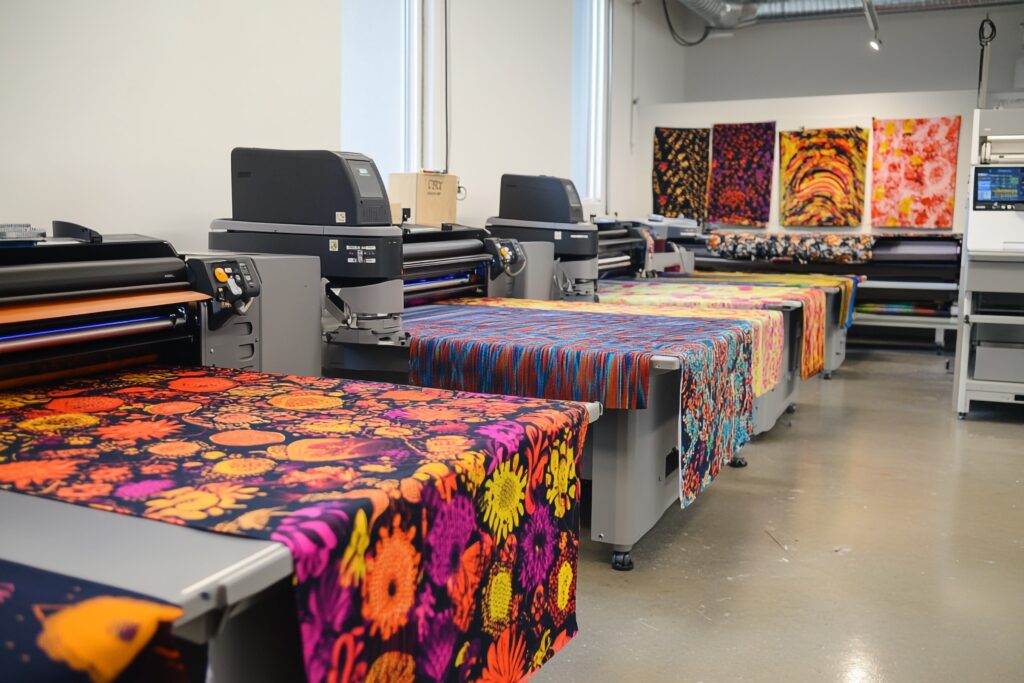
Textile industry is on the verge of a revolution in terms of technology. The digital forms of printing are making a revolution in terms of the design procedure, manufacture of fabrics and personalization of the fabrics globally. New ways of realizing sustainable inkjet, through AI-driven pattern production, are changing a large-scale industry that has mostly not changed in decades.
With this move, the manufacturers are not changing machines alone, but rather taking up a whole new approach to sustainability, production, and consumer needs. Such technological changes are significant in ensuring that businesses remain competitive and conscious of the environment.
These inventions will directly affect the work of all the textile producers, fashion designers, and investors in the industry. It is time to learn more about the latest technologies that revolutionize the sphere of textile manufacturing.
Revolutionary Printing Technologies Reshaping the Industry
Single-Pass Digital Printing Systems
The digital print technology using single-pass printing has become a game changer when it comes to large scale textile printing. This is in contrast to conventional scanning technologies that operate back and forth across fabric with the printer moving back and forth over the fabric whereas a single-pass printer can apply ink in a single pass with the textile in motion and the printheads fixed.
The technology produces very high speeds of production, and the quality of print is, at the same time, outstanding. Now manufacturers are able to produce speeds up to 100 meters per minute and the digital printing is being competitive with the older methods of large-scale production runs.
Single-pass systems also allow complex multi color designs without registration. This feature introduces additional potentials of complex patterns and gradient that could not be previously accomplished either consistently, or in some situations, at all.
Hybrid Printing Solutions
Hybrid printing is the one that uses digital and analog methods to take advantage of both strategies simultaneously. Through the same process of screen printing these systems are able to print the base colours and overlay the detail digital print.
It is a cost effective and quality approach. Screen printing of base colors offers a high level of coverage and opacity at a low price such that digital elements, which may be decorative, or some form of personalization or special effect at a high price point should otherwise be printed on their own, are possible using computer-based processes.
Hybrid systems have reduced the costs of production by up to 40 percent of some forms of designs with the manufacturers recording premium quality standards.
Advanced Ink Technologies Driving Innovation
Water-Based Reactive Inks
The reactive ink formulations that are water-based are quite a development in the printing and sustainable textile printing field. The resulting wash fastness and color brilliance is fantastic without damaging the environment, as traditional discharge inks do.
New advances in reactive ink chemistry have increased color gamut access by the printer. New inks are able to create the same colors they could only create using specialty inks such as vivid fluorescents and rich black inks.
The new improved formulations also provide better fortification and longer shelf life of the ink with reduced wastage and efficiency of production. Certon manufacturing has reported an up to 30 percent reduction in the amount of ink used and a better colour saturation.
Pigment Ink Innovations
Nanotechnology based development of pigment inks has solved most of the conventional constraints and this has been achieved due to the advancement of the binder system. The nanoscale of new pigment particles gives improved penetration of pigment particles into the fibers of the fabric and preserves the outstanding color reproduction.
The sophisticated pigment systems are more effective on a wider scope of substrates which include synthetic blends that have been very difficult to print. The enhanced capability in non-slipperiness means that printed fabrics do not fade away even with frequent use and washes.
Also, the antimicrobial properties have also been added recently to some of the pigment ink formulations for health care and activewear printing.
Sustainable Technologies Transforming Production
Closed-Loop Water Systems
Conservation on water within the textile printing processes has become an important issue. The water in closed-loop water ecosystems are recycled and cleaned, resulting in significant water reduction and waste.
Process water can now be continuously reused over and over again as up to 99 per cent of impurities are removed using advanced filtration and treatment solutions. Other plants have managed to save as much as 85 percent of their water use when compared to the conventional printing procedures.
Such systems also collect and neutralize the chemicals that would have otherwise needed an expensive northern discardation to convert waste treatment into a resource recovering activity.
Energy-Efficient Curing Systems
New curing technologies are also lessening the energy demands as far as anchorings ink to fabric is concerned. LED-based curing systems are using up to 70 less energy than traditional thermal curing and have far more uniform results.
Near-infrared and infrared curing systems also feature a very fine degree of control over temperature, allowing little damage to the fabric whilst maintaining full ink penetration. It is also accurate to print heat sensitive materials which could not earlier be handled through the digital techniques.
Certain applications have been found in some facilities to have taken solar-powered curing mechanisms; therefore, enhancing their reduced environmental impact; this is still done without quality production adjustments.
Automation and Smart Manufacturing Integration
AI-Powered Quality Control
Man-made intelligence is transforming the quality control in digital textile printing. During production, computer vision systems are able to discard the passages with defects, color shifts and pattern disturbances in real-time.
They can learn as well as each production run can be polished and will get better and better at detecting a potential problem and fix it before it becomes an expensive solution. By preserving materials that could have incurred defects in earlier implementation, early defects identified have minimized material wastage to even 25%.
The machine learning algorithms also perform ink utilitarianism and color harmony, which guarantees that the results will be reliable when passing various production runs and environmental circumstances.
Predictive Maintenance Systems
The predictive analytics and IoT sensors are changing equipment maintenance schedules. Intelligent monitoring effectively monitors the functioning of the machine, the level of ink and the environmental conditions to foresee when maintenance is required.
This will make the equipment last longer compared to the downtime that happens abruptly. Maintenance costs are reduced up to 40% with an increased improvement in overall equipment effectiveness that some manufacturers report.
Predictive systems also help in the scheduling of production since it determines the most appropriate times to carry out maintenance in order to be less harmful in delivery schedules.
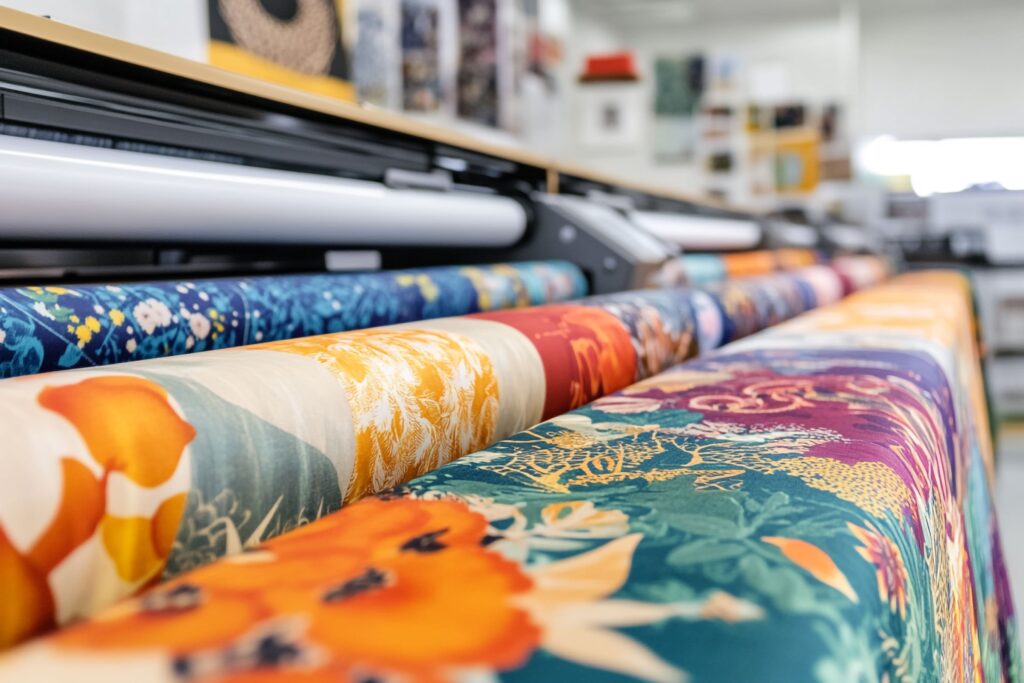
The Road Ahead for Digital Textile Printing
These new technologies have been merging in the digital textile printing process, and they are leading digital textile printing and innovating in ways never possible before. The integration of these technologies is still young, but with continued maturity, we will see even more amazing gains in efficiency, quality and environmental performances.
The extended phase of development is bound to take form in fully integrated smart factories where AI will complete the production process through the optimization of the design process, production quality solutions, and logistic control. This stage of integration will allow mass customization to be realized on scale but retaining the economies of scale of typical manufacturing.
To the professionals of the industry, it is not just optional to keep oneself abreast of these technological advances, it is the only way to be competitive in the industry. Textile companies who adopt these new forms of technology in the future are the companies who will shape the textile business of the future.