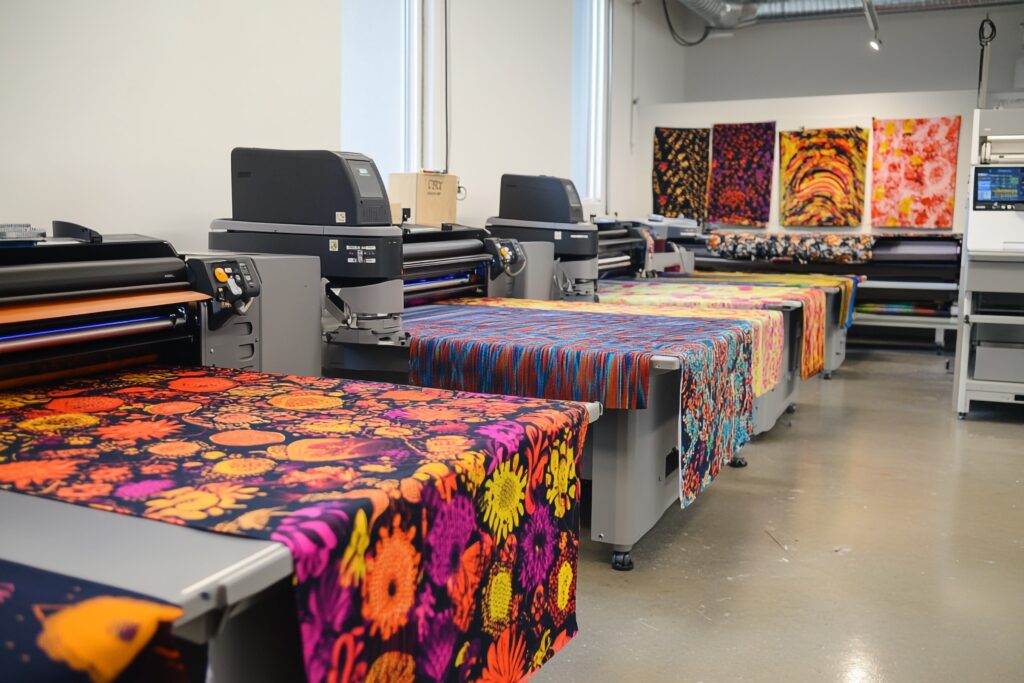
We are at a time on the road to 2025 wherein there has never been such innovation within the digital garment printing industry. Sustainable printing ideas to artificial intelligence-driven personalization, the industry is moving fast to change according to the changes in consumer needs and concern to environmental requirements. New technologies are being adopted by fashion brands, print shops and manufacturers across the world all around improving the production time and giving a high quality that is also environmentally friendly.
Knowledge of these new tendencies is important to any company that aims to remain competitive and profitable. You may be the owner of a small print shop or taking care of production in an international fashion brand the most popular trends in digital garment printing in 2025 will be shaping your attitude towards custom apparel, inventory market, and customer satisfaction.
This exhaustive manual covers the most profound breakthroughs in transforming digital textiles printing, taking a peek into the advancements being made in technologies and agendas that are already creating waves in the industry.
Sustainability Takes Center Stage
Environmental awareness is no longer a pleasant-to-add-on aspect of digital garment printing but has already become an essential one. Eco-friendly solutions are required by both the consumers and the brands and these solutions not only should not undermine quality or efficiency.
There is growing popularity among water based inks that are displacing classical plastisol inks in wide use. These recipes have lesser toxic substances and they leave gentler prints that feel less artificial on your skin. Also, the manufactures are coming up with biodegradable ink varieties, which can biodegrade in a safe way, once garments are at end of life.
The polyester substrates that are recycled are turning into a staple of large suppliers. Comprised of post-consumer plastic bottles, these materials also have high levels of print quality and minimize streams of wastes. Even the most progressive businesses are trying out algae-based fabrics that can be printed on the regular digital devices.
Another huge area of sustainability is energy-efficient printing equipment. More recent digital printers use a significant proportion of less electricity (up to 40 percent) compared with their predecessors as well as manufacturing them at a rapid rate. LED curing solutions are overtaking the traditional heat-driven curing, thus cut down energy and better work conditions.
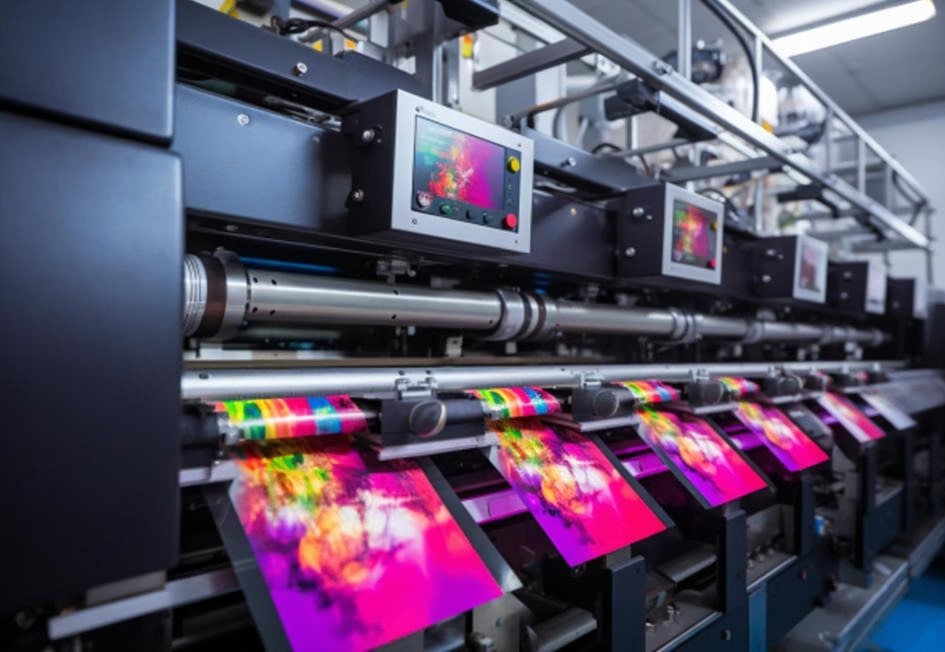
AI-Powered Design and Production
Digital garment printing is where artificial intelligence is transforming design creation, optimisation and production workflows. The current trending patterns, colours and style can now be studied by machine learning algorithms so as to provide similar designs that seem more appropriate to attract the attention of the intended audiences.
Predictive analytics may also be used to improve inventory levels as the businesses will be able to anticipate the demand concerning particular designs and colorways. The technology limits waste produced and excess production as well as keeping popular products in stock.
Automatic color matching has also become much more precise and artificial intelligence systems can auto-adjust print parameters on-the-fly to ensure a common color throughout the production of any given type of fabric. This results in much lesser wastes due to test prints and reprints.
The most advanced workflow management platforms plan all steps of production, including orders and delivery. Such systems have the ability to automatically direct the job to the most suitable equipment on the basis of substrate type, quantity ordered and on requirements of deadline.
Direct-to-Film Technology Expansion
Direct-to-film (DTF) is still on the rise as a multi-purpose alternative to conventional heat transfers. This is a technology that enables one to print on any form of cloth whether it is cotton, polyester, blends, and even on leather or canvas.
These advances in quality have been impressive in DTF printing, and the newer systems are working out prints which rival direct-to-garment quality but not limiting to that technique the flexibility of heat transfers. Vibrancy of color and wash-fastness has also improved greatly and as such DTF can be used in high quality applications.
DTF is cost effective and it is especially appealing in small to medium orders. In comparison with direct-to-garment printing, DTF does not even presuppose fabric pretreatment, which saves the materials and shortens the time of production. This productivity creates a new chance of businesses that deal with special-order apparel.
The ability to print in multi-colors without registration problems is what differs DTF with the traditional screen printing of complex designs. Photorealistic images of a complex nature with gradients can be replicated easily with an equal amount of precision that multiple screens require.
Enhanced Direct-to-Garment Innovation
Direct-to-garment (DTG) technology is still developing and getting improved in its printing speed and knot formulation of the ink. New printhead technologies allow producing output at higher resolutions but at the same production efficiency as by commercial use.
The performance of the white ink has improved dramatically with improved opacity as well as reduced hand feel when applied on dark garments. Improved ink circulation systems ensure removal of the settling and clogging problems that used to be an affliction to the DTG operations.
The automation of pretreatment is simplifying DTG processes by use of combined systems, which apply, cure and press garments automatically. The integration lowers labor cost and enhances repeatability of production runs.
Material exibility has been increased to include performance fabrics, tri-blends and specialty substrates that in the past were difficult to use DTG quality to print. New ink chemistries are coupled well to moisture-wicking fabrics and they remain flexible after repeated wash treatments.
On-Demand Manufacturing Growth
The gradual transition towards on-demand production processes continues to speed up with brands even willing to take the risks of not filling their inventory completely and have a possibility of reacting to market fluctuations. Digital printing technology allows low-volume production economically, and this has allowed on-demand to work with mainstream brands.
On-demand models are establishing local production networks, which induce cost saving on shipping cost as well as transportation time and strengthen regional economies. Such networks take advantage of the flexibility of digital printing to take care of several brands using the same plant.
Mass customization enables the brands to provide customization to their products without facing the customization penalties. Shoppers may decorate colors, type in a text or even choose among the design variants and make receive reasonable prices without delays of transfer.
On-demand production ensures inventory optimization, which also assists brands to minimize the cost of storage and dead stock. It is also possible to reprint those designs that are popular and also to discontinue the ones that are not moving that fast without a lot of impact to the budget.
Advanced Finishing Techniques
Digital printing is moving beyond simple applications of ink to encompass finishing effects that once only specialty process could provide. The digital printing equipment manufacturers are beginning to standardize with metallic inks, fluorescent colors, and textured areas.
The dimensional printing textures add the level of touch to the printed textile by creating raised printing textures. These effects are possible using special inks, or after printing processes which add value to the perceived cost of final products.
Combination methods In this case, our digital printing technique is combined with such traditional printing as embroidery or screen printing to produce a hybrid that has never been made before. It is possible to automate those various processes to achieve efficiency and open up new modes of creativity.
Automation in quality control assures good quality and reduces labor in prints, as the computer vision in quality control checking output defects. Such systems have the ability to test changes in color, printing defects and location faults human judges may miss.
Embracing the Future of Digital Garment Printing
The most significant trends in digital garments printing 2025 are not only technological progress, but the fact that ultimate reality portends a transition in production approaches to the more sustainable, efficient, eco-responsive pattern. The key to success in this changing environment is adopting the new technologies and at the same time not forgetting about the services and customer satisfaction.
Companies investing in the sustainable printing solutions, AI-augmented optimization and flexible production capabilities will be most prepared to succeed. With these trends being integrated in the business, a new opportunity has been developed to achieve better profitability in the light of increasing consumer expectations of environmental responsibility and customized products.
Begin assessing what trends will match your business objectives and demands of clients. You may also consider collaborations with equipments suppliers and ink manufacturers that are at the forefront of innovation in these areas in order to make sure, that you are ready to the further evolution of digital technology of garment printing.