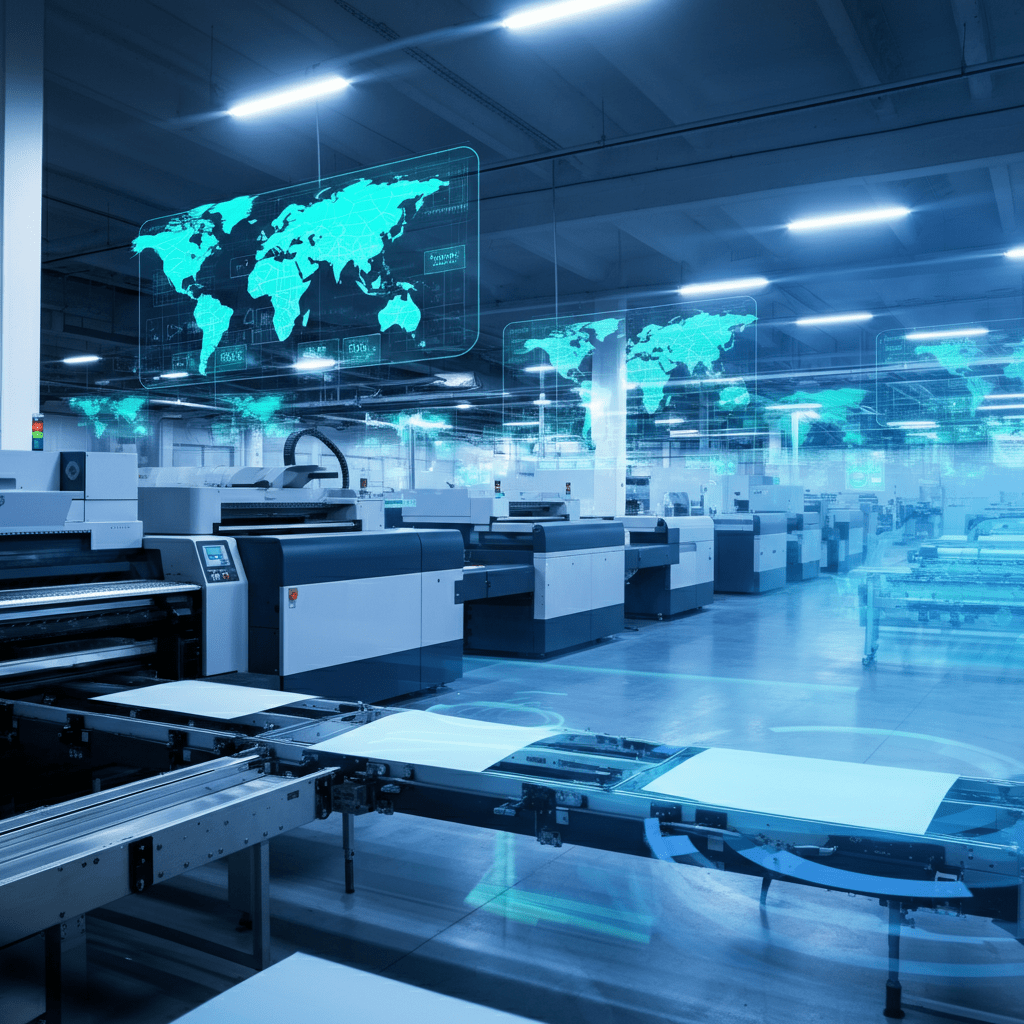
How to Master Workflow Optimization for Large-Scale Print Production
The massive facilities that deal with print production take care of thousands of tasks every day and include marketing materials as well as packaging elements. And with this degree of volume, there arrives the factor of complexity, to maneuver deadlines, to coordinate resources, and to ensure standards of quality throughout various projects at one point in time. When it comes to workflows, their efficiency almost always determines the profitability of an operation compared to the one struggling to reach margins.
Optimisation of workflow operations in large scale printing refines chaotic operations to fine-tuned systems which minimise wastage, turn around time and increase profitability. This is not the partial way of looking at each step of the journey of receiving the job till the job is delivered with bottlenecks being looked at with solutions being introduced that can scale up with the progression of your operation.
Understanding the Foundations of Print Production Workflow
Good workflow optimization should start by drawing a map of your existing processes. Large-scale operations usually require several departments such as prepress, production planning, press operations, finishing and shipping, each department having different responsibilities and deadlines. Owing to an evaluation of the way these departments relate with one another, there is room to enhance matters.
Any optimized workflow is based on three pillars, including standardization, automation, and communication. The standardization patterns are maintained through standard methods between shifts and operators. Automation minimizes tedious job requiring subjectivity and time lag. Effective communication lines eliminate occurrences of uncomprehended messages that culminate into the hustle of reprints or delayed delivery.
The majority of facilities find that their processes have developed as the organization grew with no formal design and have become inefficient, and then inefficient processes multiply as volume of work grows. A systematic review can reveal the unnecessary steps, states of confusion at transition points between departments and the manual steps that can be automated.
Implementing Technology Solutions for Workflow Management
Integrated systems software play an important role in modern workflow optimization of large-scale print production. The management information system (MIS) is referred to as its central nervous system, which tracks the jobs through estimates to delivery and gives real-time access to the status of production.
Web to print portals make order entry and minimise administrative overloads. Customers are able to present jobs, sign off proofs and view statuses without using the staff time. These systems are integrated into prepress workflows and maintain approval of jobs and automatically routes specification- and capacity-based production routing into production queues.
With automated scheduling systems, the use of automated presses is optimized according to the needs of the job, material and also deadlines. Complex algorithms would allow pooling of identical jobs to reduce setup delays, equalize hoops on devices, and alert possible conflicts soon before they have a production effect.
Color management systems guarantee uniformity between several presses and substrates. Other technologies such as automated plate imaging and direct-to-press technologies disable all the manual work without compromising quality. The digital job tickets are carried with every project, which gives the operator all the specifications with fewer chances of mistakes during set up.
Optimizing Prepress Operations
The largest bottleneck in large scale activity is normally in prepress department. Check out that several conventional prepress procedures, such as file processing, and the production of plates, can be automated by the application of digital workflows. Preflight systems identify issues before they could cause problems once they are in the production level.
Uniform file formats and submission requirements lead to the decrease of preprocessing time. Automated hot folders organize the incoming files according to job type or specification and redirect them into relevant workflows without any need of manual handling process. Version control systems avoid confusion when customers make submission of several revisions of files.
Workflows can be organized around a templated workflow to speed up standard types of jobs such as business cards, brochures or packaging. After being made, these templates automatically apply proper specifications, obligate layouts, as well as produce a ready-to-production file where the intervention of an operator is limited.
Automated color separation and proofing also guarantees consistency and helps decrease the number of manual touch points. Remote proofing systems enable the customers to go through the job and approve it electronically thus no shipping delays or physical proofing costs.
Streamlining Production Floor Operations
The task of the production floor optimization is directed to maximize the use of equipment keeping up the quality of production. Solutions that run in real time keep an eye on press performance and flag areas of maintenance before resulting in unplanned downtime. Changeover operations are automated which latentiates setup between jobs.
Kanban systems control and regulate the work in progress inventory and this means that materials flow freely throughout the production without generating any congestion. Visual management boards also keep the supervisors informed on the spot as to which areas are a problem and which need attention.
Cross-training of operators makes it more flexible since the employees can move across the types of equipment depending on the workload. Standard operating procedures provide consistency in the outcome in that the outcome will be the same even with which operator is performing a specific job.
Check points for quality control establishment within the workflow picks up problems at an early enough time to avoid widespread reprints. The statistical process control systems monitor quality parameters over periods and may find patterns resulting in poor quality.
Coordinating Finishing and Post-Production
Such mass printing projects usually presuppose the complicated procedure of finishing: cutting, folding, binding, or packaging. This engagement has to be scheduled in such a manner that they are in line with press schedules so as to avoid either a bottleneck or excessive work-in-progress inventory.
Utilization of automated finishing machines in combination with production scheduling systems streamlines the flow incurring less labour cost. Bar code tracking systems help in the proper job routing when there are several finishing steps and hence mix-ups are avoided and may lead to wrong deliveries.
Delivery of materials is done on a just-in-time basis in line with productions reducing the cost of carrying inventory yet the materials remain available whenever needed. Production forecasts have the ability to generate purchase orders of consumption goods automatically with the help of the supplier integration systems.
Measuring and Improving Performance
Improvement of large-scale print production workflow should be a process of constant measurement and enhancement. The efficiency measures that should be monitored by means of key performance indicators are overall equipment effectiveness, job cycle times, and first-pass quality rates. Income indicators, such as the profitability of jobs and the use of resources supply extra reporting.
Data analytics platforms can specify patterns and trends which could otherwise be overlooked manually. Predictive analytics allows determining the capacity in advance and determining areas of the possible accumulation of bottlenecks, until they become manifested in the customer deliveries.
Audits of the work enable this to be done regularly and business conditions keep processes optimized. The customer feedback mechanisms are a great way to learn how the delivery performs and how it is perceived in the quality term.
Scaling for Future Growth
It has to support growth with no increase of overheads in optimized workflows. When compared to cloud-based systems, scalability does not have any serious capital investment. Facilities can improve the functionality of their systems due to changing needs because of modular software architectures.
Automated reporting systems offer the position of management real-time access to operations, which assist in data-based decision making. Integration is the ability to make new equipment or software interchanged with the already existing systems.
Employee training plans ensure that employees are in a position to utilize streamlined processes well. The process of managing change assists in establishing improvement in an efficient way without any interference in production.
Transforming Your Print Production Future
Print production workflow optimization in mass printing changes operations into proactive work, rather than working in fire brigade mode. The competitive edge goes further than efficiency–enhanced customer relations, better quality production and greater profit will lead to a long-term success.
The first step should be to carry out a thorough audit of your workflow so that you can know your greatest opportunities. Ensure that you first get the easy bottlenecks out of the system even before doing advanced automation. Do not forget that optimization needs technologies, as well as the organizational intention to grow constantly.
The rewards of your workflow optimization investment take the form of decreased wastage, accelerated time to turn around and enhanced customer satisfaction. Any companies, which streamline their operations, will be well placed to benefit as market demands keep shifting to shorter delivery lead times and greater customization.