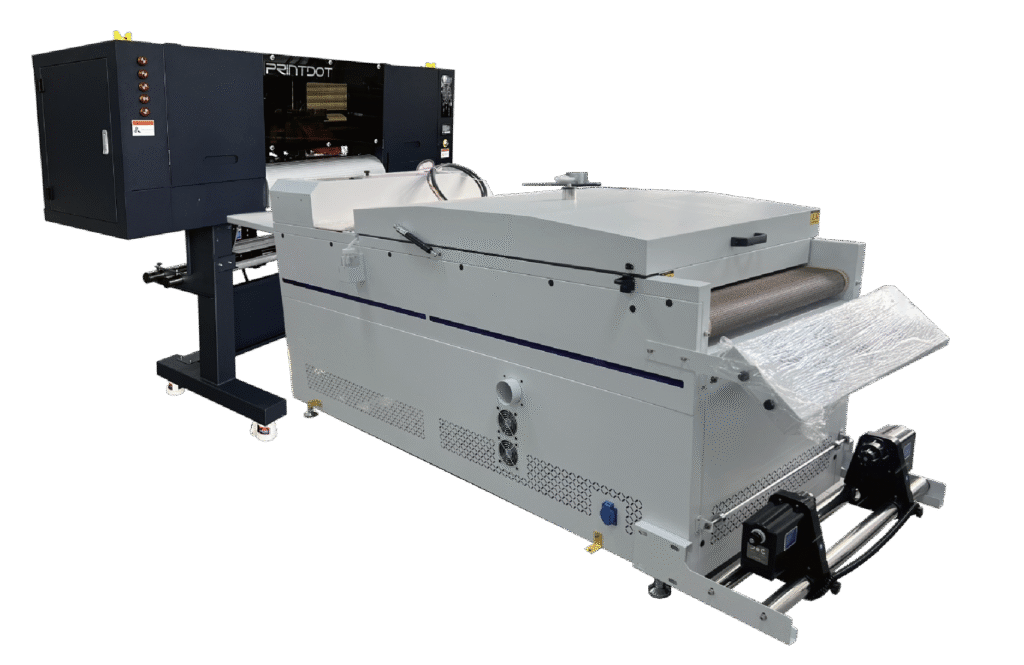
Direct-to-film printing has transformed the personal clothing sector, which is quite a simple method of producing lively long-lasting designs on a variety of fabrics to companies and even hobbyists. DTF printing can be done in countries that traditionally practise screen printing or vinyl cutting, you can also use DTF to transfer complicated designs on to the garments by means of adhesive powders and films.
This ultimate beginner guide to direct-to-film printing will take you through all you should know about direct to film (DTF) printing process. Learning how to work with the basic equipment and perfecting both the transfer method and the technique, you will understand why this printing style is gaining more and more popularity both with entrepreneurs and small companies and with those people who simply love printing.
It does not matter whether you want to open a custom t-shirt company or just enjoy making personalized products to your friends and relatives, DTF printing can help because it provides flexibility and quality that is hard to beat in other printing technologies.
What is Direct-to-Film (DTF) Printing?
Direct-to-film printing is a technique of digital printing: printing by means out a special PET film, adhesive powder, drying the print and heat pressing the print to the material. DTF printing produce a soft, washable transfer which bonds directly to the garment.
The technology was an answer to the constraints common in direct-to-garment (DTG) printing and heat transfer vinyl (HTV) print encoding. The DTF printing process supports most kinds of fabrics cotton, poly, blends and even difficult fabrics nylon, even leathers.
The difference about DTF technology is that it can print in full color including fine lines, gradients and photographic quality without any weeding and complicated color separations. The process has also saved the pretreatment of the fabric which DTG printing usually requires.
Essential Equipment for DTF Printing
DTF Printer
A converted inkjet printer with DTF inks is the heart of any DTF set up. Most popular would be converted Epson EcoTank models such as the L 1800, L 805 or professional DTF printers such as those by Epson, Roland or special DTF equipment providers.
These printers are specially designed using water based pigment inks intended to print DTF. The inks normally consist of cyan, magenta, yellow, black and white color, although it is vital to have the white ink when one wants to get bright colors on a dark cloth.
DTF Films
It is a special coated PET film which is specially intended to accept DTF ink and then when heat is applied to cleanly transfer the image. These movies have different thickness levels and different coating formulae with most being between 75 and 100 microns thick.
The DTF films maintain high quality of ensuring that the ink is absorbed, no bleeding of the ink and smooth handling of the film during heat pressing.
DTF Adhesive Powder
The bond is achieved by hot melt adhesive powder-provided polyvinyl chloride. This powder is a thermoplastic that is melted in the process of curing and pressing forming a washable adhesive and flexible layer.
The powder comes in different formulations with different types of fabric and washing. A finer mesh of powders tends to offer a superior degree of hand feel and flexibility.
Heat Press or Conveyor Dryer
To provide a printed film, both a good heat press and a conveyor dryer are critical to both the curing process and transferring of the designs to the garments. Temperature and pressure are determinant of attaining good adhesion and durability.
Most DTF applications require temperatures between 280-320°F (138-160°C) with medium to firm pressure for 10-15 seconds.
Step-by-Step DTF Printing Process
Step 1: Design Preparation
Design or draw your own design with the help of graphic creation programs such as Adobe Illustrator, Photoshop or free version such as GIMP. Make your design print ready at correct resolution (300 DPI or more) and correct color profiles.
Before printing your DTF designs, unlike screen printing, the designs ought to be positive (this is not mirrored). Apply white underbase layers in design meant to be printed on dark grounds so as to brighten the colors.
Step 2: Printing the Design
Take your DTF film and load it into your printer with the coated side down on the print heads. Send your print through DTF specific ink profiles and settings. The majority of the designs usually need an underbase(white ink) that has been printed, then the colored layers are printed.
The printing environment should have the right level of humidity (45-55%) to avoid the bleeding of the ink and to achieve the best results.
Step 3: Powder Application
Put the DTF adhesive powder in the printed place when the printing ink is wet. The powder sticks on wet ink and forms the adhesive cover that will stick to the fabric.
Get rid of the extra powder and get it ready to use at another time. Wash durability and transfer adhesion requires good powder coverage.
Step 4: Curing the Print
Cure the powdered print using a heat press, conveyor dryer, or curing oven at approximately 338°F (170°C) for 2-3 minutes. This process melts and sets the adhesive powder, preparing the transfer for storage or immediate application.
Transfers are supposed to be properly cured and can be kept until months before they can be applied, which makes DTF suitable in terms of inventory.
Step 5: Transfer Application
Position the cured transfer onto the garment and apply heat and pressure using a heat press. Typical settings range from 280-320°F for 10-15 seconds with medium pressure.
The carrier film should then be removed after the transfer is cooled. There are occasions when a cold peel would be quite necessary, whereas warm peel removal is most efficient with other transfers.
Advantages of DTF Printing
DTF printing is advantageous in many ways such that it is appealing to new and seasoned printers. It is a relatively fast process that can be applied to a wide range of fabrics without the need to first be pretreated and is unlike DTG printing that normally requires the application of special solutions so that the ink will adhere well to the material.
The other significant advantage is related to production flexibility. It allows printing of transfers so that you can use them when necessary hence easier to keep stock and handle orders conveniently. This setting with the ability of batch production is especially useful to small businesses.
DTF is also the print making process that would give you sharp, colorful printing with good wash cycles provided it is done right. Colors do not fade easily and the designs still keep their originality even after several washings.
DTF is also the print making process that would give you sharp, colorful printing with good wash cycles provided it is done right. Colors do not fade easily and the designs still keep their originality even after several washings.
Common DTF Printing Challenges and Solutions
Powder Adhesion Issues
The cause of poor powder adhesion is usually poor ink setting, insufficient humidity or dirty films. Make sure the printer conditions to be optimized to use DTF inks, and correct environmental conditions.
Transfer Durability Problems
The usual causes of wash durability are poor curing temperatures, low producing pressure at the time of application or powder incompatibility. Check your calibration of equipment and material specification.
Color Accuracy Concerns
Consistency in colors can be achieved by ensuring printer profiling and maintaining it. Regularly clean the print heads and use good quality of DTF inks that are supplied by trusted suppliers.
Getting Started with Your DTF Journey
Beginning with DTF printing should be planned carefully and investments into the quality equipment are necessary. First of all, look out good suppliers of printers, inks, films, and powders. Competitors provide starter kits that contain all products required to engage in initial experiments.
You might as well begin working with a smaller format printer to learn the process and then invest in bigger and more costly ones. You should try a wide range of fabric types and level of design complexity to get a grasp on what your setup can and can not do.
Enter into internet communities and message groups that revolve around DTF printing with experienced users who will guide you, help you fix up your problems, and suppliers. The DTF printing community as a whole is friendly and open to the idea of making a beginner successful.
Develop the basics and then spread your operation. Quality and stable processes are worth more than being in a hurry to build up the volume of production.