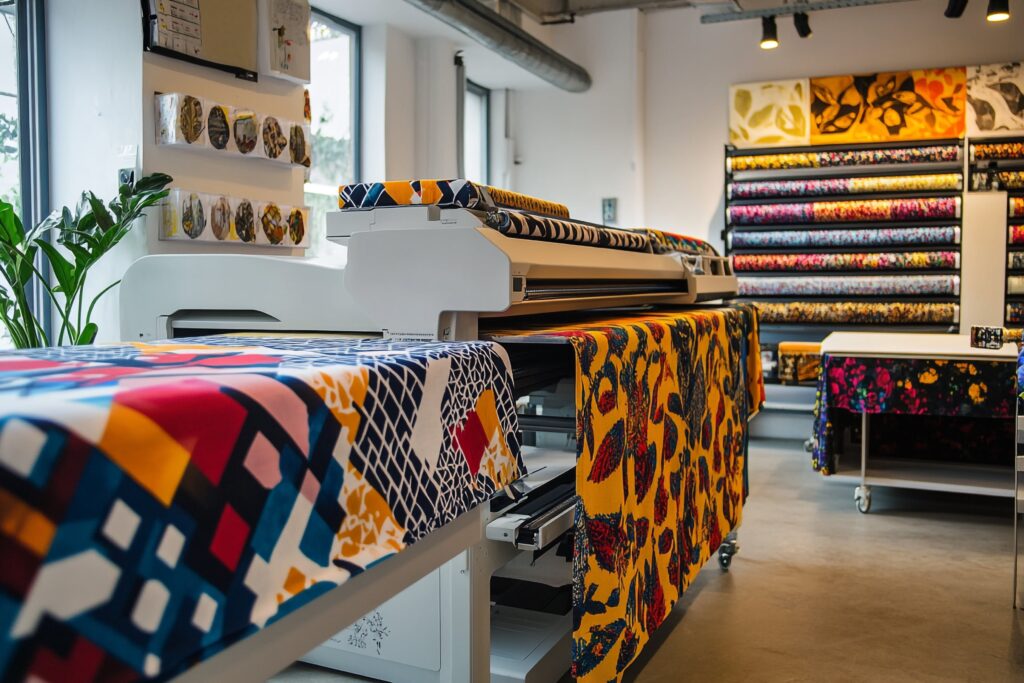
The printing sector has undergone a spectacular change in the last ten years, the various ways in which this was done were even sought to replace the traditional ways. Screen printing and Direct-to-Film (DTF) printing are two well-known rivals in the field of custom apparel and textile printing. Both solutions have entailed unique benefits, and, therefore, it is of utmost importance to businesses and individuals planning on printing high quality documents to assume which solution to use.
Knowledge of merits of direct-to-film (DTF) print and screen printing will help you make a right decision regardless of production requirements, financial factor, and peception of quality. This inclusive guide looks at the two technologies, application, costs and performance characteristics so that you can make out all the better the kind of printing technique to adopt in fulfilling your demand.
As a new or already well known apparel company, a printing shop in search of finer prints, or an individual look into custom print services, neither DTF nor screen printing direction will have less influence in the business outcomes of its operation, product, or bottom line.
What is DTF Printing?
Direct-to-Film printing is a fairly recent strategy of textile covering that has recently gained much popularity. The newly developed process is not only the addition of adhesive powder used with wet ink which is applied on a special film through the printing of designs with the help of water-based inks. The film is then dried and transferred onto the fabric with use of heat and pressure.
DTF process starts with designing a digital printing and again it is printed in reverse by special DTF inks onto the PET film. Such inks are designed to be used in the DTF transfer process, which is why they perfectly adhere and last long. Once printed, the wet ink is treated with hot-melt adhesive powder so that, in the future, it would glue the design to the material.
Another most attractive feature about DTF printing is that it is versatile. Contrary to other printing methods working on a limited paste of fabrics, DTF can be used on cotton, polyester, blends, leather and even stretchy hard surfaces. It is this adaptability that makes it a great choice to businesses that deal with a wide range of customers, or individuals who use different types of materials.
What is Screen Printing?
Silk screening or screen printing is an old technique of printing popularly applied to many years of textile businesses. This is a method in which, a series of stencils (or screens) is made in each colour of the design and the ink is pressed through the screen mesh onto the fabric with the aid of a squeegee.
Screen printing is time consuming in regard to manufacturing time and preparation. Any color in a design requires a single screen and it has to be photo emulsified and well positioned with respect to proper color registration. The screens are then attached to a printing press and inked applies in turn through the screens to form up the entire design.
Screen printing is best used in high producing runs in which the design is printed hundreds or thousands of times. The upfront cost and time will prove cost-effective when it is divided into huge numbers, and this is the reason why major apparel brands and large-scale business activities prefer to choose it.
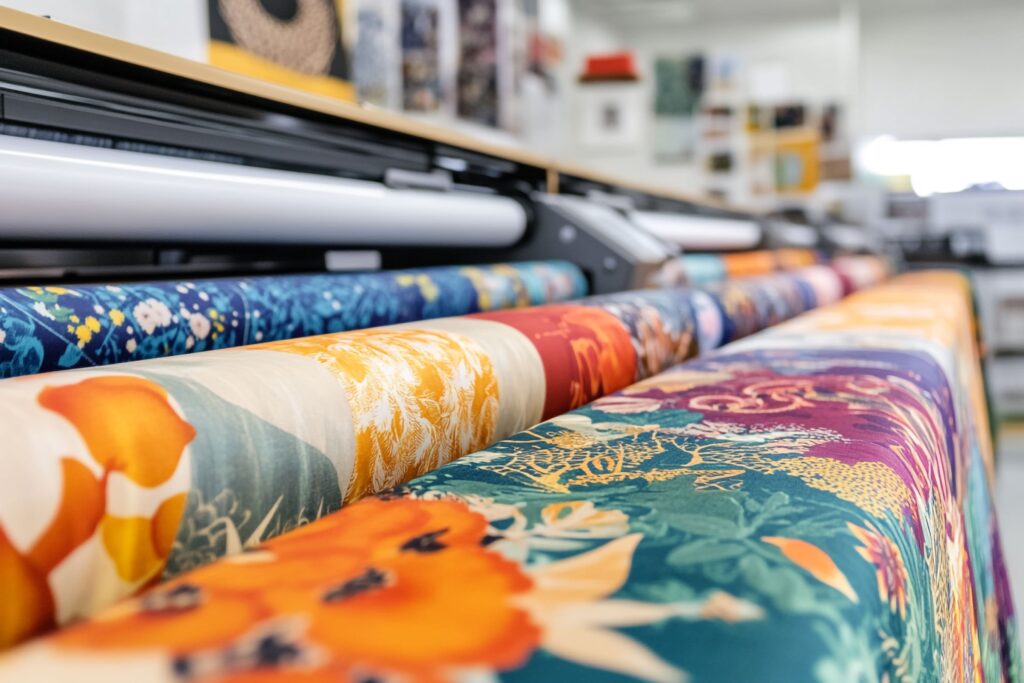
Key Benefits of DTF Printing
Superior Color Vibrancy and Detail
DTF printing gives outstanding color and fine detail performance that even outclasses the abilities of many of the traditional printing processes. Its digital process enables it to accurately color match and be able to render intricate designs with gradients, photos and other complex patterns that could not be created or would have been difficult to do on a screen printed material.
The unlimited color capability of the DTF process doesn t incur any extra set up expenses and is suited towards design/art work with high volumes of colors. It presents the designers with new opportunities to be artistic since before designers were limited to simplify their artworks by the constraints of screen printing.
Minimal Setup Requirements
Among the greatest merits of DTF printing, it requires minimal setup. DTF printing does not need screens, squeegees or long preparation times, similar to screen printing, giving it the ability to start production nearly instantly after the digital artwork is received. The efficiency also means that the turnaround time is reduced and that it can easily take rush orders.
The digital workflow also avoids necessity of physical stocks of screens and the area that is needed to set the production up. The simplicity of this process, however, is why DTF printing is especially suitable in organizations with less space or those concentrating on semi-custom print-on-demand orders.
Cost-Effective for Small Runs
DTF acts as an excellent alternative to screen printing in terms of small volume production runs which screen printing may become too expensive. DTF does not require any screen preparation and set up cost and can sell individually or in small production. Such an advantage renders it suitable to custom orders, or prototypes, as well as limited-edition designs.
On-demand printing eliminates the inventory danger and the expense of keeping stock in the warehouse. The advantage is that the businesses are able to manufacture items in accordance with orders, and they do not have to store massive amounts of pre-printed items that nobody might buy.
Versatile Fabric Compatibility
DTF printing can be used on a very wide set of fabric types and colors and even on dark fabrics that have been difficult in the past to print using other systems. The DTF transfer gives a translucent coat through which the bright paint is clearly visible on the light and the dark base without any specific base requirements and pre-treatment.
This flexibility applies also to fabric composition. DTF transfers combine easily with cotton, polyester and Poly-cotton mixes and even some synthetic materials thus it can be used on a variety of garment types and applications.
Key Benefits of Screen Printing
Unmatched Durability
Screen printing is the assured designation of durability in textile print. The deposits of the thick ink and bonding by chemicals via the screen printing process make the prints capable of resistance to hundreds of washing use with the prints still possessing the print as they were before, and in its whole integrity. The durability of screen printing makes it the most preferred option in work wear attires, uniforms, and products that will be subjected to heavy use.
Screen printing using plastisol based inks forms a flexible permanent affinity over the fabric which is resistant to cracking, peeling off and fading. This strength is especially useful to things that will be washed a lot or under extreme conditions..
Superior Economics for Large Runs
The more that is printed, the more the cost effectiveness of the screen printing becomes. Though the initial fixation cost could be big, the cost per unit progressively reduces significantly as the volume increases. Screen printing can make more economical sense than DTF printing above runs of 50 pieces, in particular on simple designs with few colors.
Screen printing is also economical when printed in large quantities due to their speed of production. Use Once installed, it is very efficient in mass production with skilled operators able to produce hundreds of pieces an hour.
Excellent Ink Opacity
Screen printing is high in ink covering especially when used in dark colors. The opaque color which is obtained through thick ink deposits that is possible with screen printing appear vibrant and covers the color of the underlying fabric fully. The other printing techniques do not wield much success in producing this kind of opacity and it has retained to be one of the strongest features of the screen printing technique.
Specialty inks can also be printed as an advantage of screen printing. The choices are metallic inks, glow-in-the-dark formulations and puff inks which produce raised textures and discharge inks which removes fabric dye and furnishes a deposit of color.
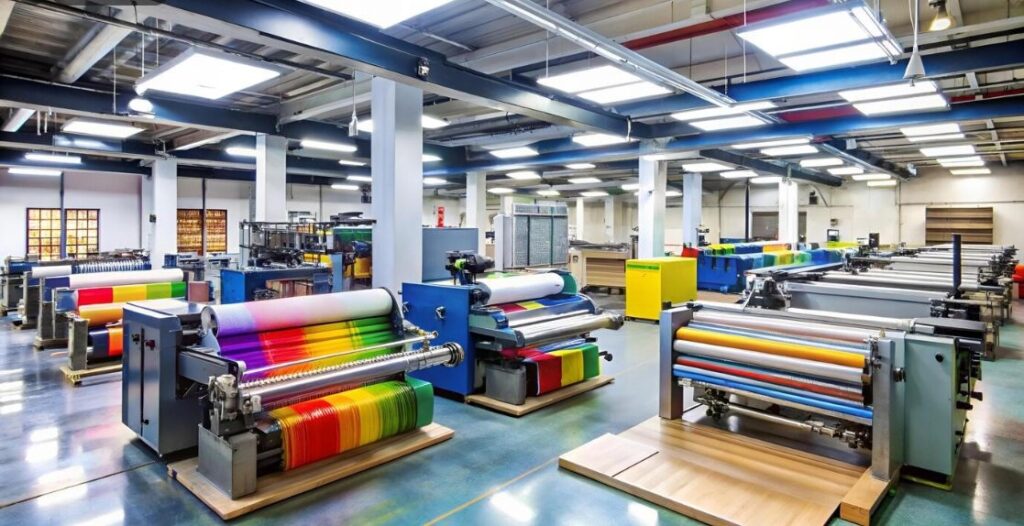
Comparing Print Quality and Durability
Comparison of print quality in DTF and screen printing indicates that each of these processes has individual features. DTF printing is best in reproduction of fine detail, gradients, as well as reproducing photographic images with gradient color transitions. Digital printing process has the capacity to produce high-resolution prints grasping the little aspects of design that screen printing would not otherwise be able to achieve.
Screen printing, nonetheless, renders strong, rich colors of excellent opacity, and a heavy hand-feel. The heavy ink layers leave prints that are both solid and strong, which is an added feature that most shoppers identify with well-made screen-printed garments.
Screen printing also dominates in wash-fastness and long -term wear resistance as indicated by durability testing. DTF prints are tough but might wear out more quickly than print screen products, especially at the edges of a design, or anything that is used a lot and stretched repeatedly.
The texture of the print varies a lot when it comes to the two methods. DTF transfers are a thinner more flexible print which drapes much closer to the natural drape of the fabric. Screen printed as compared to digital printing gives a thicker texture which some customers may want due to a perceived quality and durability.
Cost Analysis and ROI Considerations
In cost analysis it is clear that the decision whether to go with DTF or screen printing basically depends on an order quantity and complexity of the design. In small runs (1-50 pieces), economics are often better with DTF printing as there is little or no cost of setting up and complex designs are printed without any extra fee being charged.
Screen printing is cost effective when print runs are large and it is generally changed over at quantities of 50-100 prints depending on the complexity of the design, and the number of colors in the design. Cost of set up is relatively expensive under screen printing, but this is spread over a larger number of units lowering the cost per piece significantly.
Labor expense is also not the same within the methods. DTF printing is also much less labor intensive per printed piece, but skilled labor is required. The screen printing process needs proficient press operators and possibly a greater amount of manual manufacturing ability, especially when a multi-color design should be printed, where accurate registration is needed.
Different methods involve vast differences in terms of equipment investment. DTF printing needs different printers, inks, films and sticky powders to be used and the low-end varieties cost about 15 000 -20 000 dollars. Screen printing machines may consist of the simple manual presses priced under $1,000 to the more complicated auto-press costing between $100,000 and more.
Production Speed and Efficiency
Compare and contrast of the production speed has revealed that both methods are preferable in certain situations. DTF printing is quick to set up and can also start printing within minutes of taking in artwork. Digital workflow also gets rid of a lot of preparation to be done during screen printing.
Where the print order is of individual items or small runs, it is usually quicker on a total turnaround basis to use DTF printing. DTF is also extremely efficient with custom orders or custom product lines since the ability to print different design sons in a row without any changeover time.
Screen printing is high-speed in the production of high quantities of similar products. When the set up is done well, highly skilled operators are able to work at hundreds of pieces per hour, which is infinitely more than DTF printing could do with the same design.
Effectiveness takes the printing speed as only a factor but also touches on the utilization of materials, energy and labour usage. DTF printing produces little waste product and less physical area is needed, but screen printing can result in more material waste during setting up and cleaning up whereas large orders have a higher throughput.
Environmental and Sustainability Factors
Coming to environmental impact comparison, there are significant aspects that businesses that are conscious of sustainability do not need to overlook. The inks used in printing DTF are water based which can be said to be less harmful to the environment compared to plastisol ink typically used in screen printing. There is also reduced waste production in the production process being that there is minimal waste of inks not to mention no screen cleaning chemicals are required.
Screen printing of particularly plastisol type of inks use more chemicals and creates more wastes in screen preparation and cleaning. Nevertheless, a longer life of screen-printed objects can partially counteract some environmental influence because products will be used much longer.
Production of energy varies depending on the technique applied; the DTF method consumes much energy when it comes to the curing process, whereas the screen method will need some energy whenever it comes to ink curing and preparation of the screen. Total environmental repercussion varies with a special equipments, yield and local power sources.
Considerations in waste management are film waste during the DTF printing and the screen preparation waste in screen printing. Both print processes need adequate systems of disposing inks and chemicals, though many will find out that DTF printing is less hazardous.
Which Method Should You Choose?
The type of printing selection between DTF printing and screen printing relates to a number of important factors which fit into your business scope and production. Look at DTF printing when your work deals with small-quantity order, short turnaround time, complex or highly detailed design and when you want to print on diverse kinds and colors of fabrics.
DTF printing is perfect when custom orders are oriented, print-on-demand services, or prototypes. The flexibility of the technology and the low necessities to establish it makes it ideal when the companies have the necessity to quickly react against any changing market need or demands by the consumers.
Select screen printing, where large quantities are frequently handled, the utmost hardwearing is needed, where the design is uncomplicated and may not need a wide variety of colours or where cheapest possible costs per-unit are needed in high-volume manufacturing. Screen printing is still the most suitable option of well established brands that require and demand a constant high repetition.
Most of the businesses that are successful in printing have both these technologies working on them with DTF being used to make small runs and complicated designs and screen printing being used to make large runs. This combination or mixed solution is highly effective in terms of efficiency and enables different businesses to satisfy various customer needs as well.
Maximizing Your Printing Success
Whether doing screen printing or DTF, it is necessary to know what the technology is and is not capable of in order to streamline your work process, making working with it enjoyable and hassle free. It is also important to invest in the right training of your operators since skilled technicians have a great influence on the quality of printing and the efficiency of production.
When choosing technology make decisions that are dependent on your target market and business model. DTF printing is suitable to companies that are based on personalization, fast manufacturing, and a variety of products. Screen printing is the best print method when there is predictable mass production and the customer requires the products to last long, not cared for aesthetics.
Keep updated with the technologies in both fields since equipment, inks and processes are constantly being developed. Periodical maintenance and training of operators helps maintain quality and will save you optimum returns of your investment.
Establish a network of trusted suppliers of consumables because the quality of your end product is directly related to the quality of your ink and material. When comparing the financial performance of each method, you have to consider the total cost of ownership that consists of equipment depreciation, costs of maintenance and consumable costs.
DTF printing has its useful aspects when comparing to screen printing, as does screen printing with its useful aspects in different business models. When you know the advantages that direct-to-film (DTF) printing has over screen printing, you can make informed choices based on what fits your unique needs and budget as well as what fits your requirements on the quality front. The secret of the success is in selecting the best technology to your specific case and optimize your practices to provide the top outcomes to your customers.