Every Operator Should Know
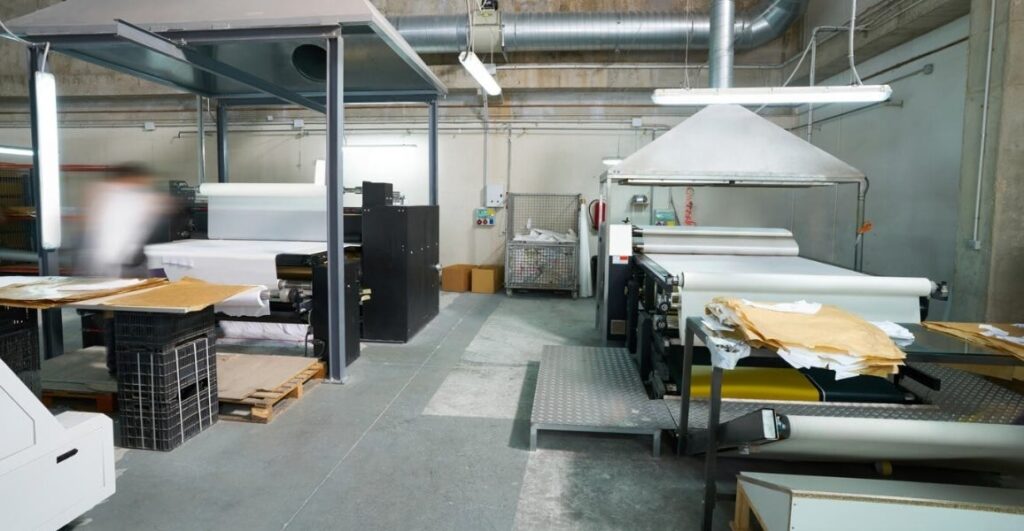
Heat transfer roller machines are an effective and potent industrial tool that can revolutionize productivity in your production levels, and yet they are a dangerous product which can cause significant harm to safety when mishandled. Whether you are producing vinyl transfers, sublimation prints, or other textile applications, compliance is not the main concern when it comes to the topic of understanding and enforcing proper safety procedures; it is a matter of life and limb and avoiding very expensive mistakes.
Incidents that cause workers to suffer third degree burns, crush injuries, and damage to equipment as a result of industrial accidents that involve the use of heat transfer equipment can easily be avoided in case safety standards are adhered to. The positive thing was? Most of these accidents can be prevented altogether in case operators adhere to the safety standards and safety-sensitive culture.
This book is a detailed one on the precautions of the heat transfer roller machine which should be known by the operators, supervisors and facility managers. We will take you through all the necessary procedures that will help you ensure that your operations run smooth and above all make your workplace safe everything; including pre-operation inspection and what to do in cases of emergency.
Pre-Operation Safety Inspections
The best way to prevent accidents is to carry out a pre-operation check before firing any heat transfer roller machine. It is like a systematic check that should become second nature to every operator.
Begin by inspecting the roller surfaces to see whether there are any damages, wear or debris. Worn rollers will render additional pressures uneven, and the result is either jamming of the materials or unforeseen machine movements. Ensure that all safety guards and protection barriers are firmly fixed and are working appropriately.
Check the electrical terminals and power cords to be frayed, have exposed electrical wires or are not securely beaten. The machines used to heat transfer consume a lot of power and electricity faults may cause electricity fire or electrocution. Ensure there is a readily accessible emergency stop buttons, test the emergency buttons when carrying out inspection.
Special pre-operation attention should be paid to temperature control systems. Make sure that thermostats and temperature display work properly, and that overtemperature protection devices are activated. Failure of temperature control may lead to overheating and fires or even burns of operators.
Personal Protective Equipment Requirements
The proper personal protective equipment (PPE) is the last line of defense in protection against injury to the heat transfer roller machines. Heat-proof gloves with the safety rating that corresponds to the operating temperatures of your particular equipment is not optional. Nevertheless, wear gloves that fit snugly and may not stick in moving equipment.
The use of eye protection becomes very important when handling hot materials which can form fumes or dust. Most applications are covered by safety glasses with a side shield or goggle, although specialized face shields are sometimes required by high-temperature work.
Heat proof aprons or coveralls guard your chest and arm against getting in a hot surface. Select materials which will not melt or inflame at the temperatures you are working in. Slip resistant soled closed-toe footwear is required – make sure not to use open footwear, sandals or loosely fitting footwear to operate heat transfer equipment.
Depending on the materials you are working with you might need respiratory protection. Certain adhesives and materials release vapors, which is toxic when inhaled, after heating. Check your material safety data sheets and use good ventilating or respiratory protection where necessary.
Temperature Control and Monitoring
Proper temperature management is crucial for both product quality and operator safety. Heat transfer roller machines typically operate at temperatures ranging from 250°F to 400°F or higher, making temperature control a critical safety consideration.
Never rush your equipment to operating temperature, always warm-up. Sudden variations in temperatures may provoke thermal strains on the component parts and conditions turn hazardous. Rheostat monitors the temperature continuously throughout the operation and checks up any abnormal fluctuations without delay.
Establish clear temperature limits for different materials and applications. Exceeding recommended temperatures can cause materials to ignite, release toxic fumes, or create other hazardous conditions. Train all operators on the maximum safe operating temperatures for your specific equipment and materials.
Accept periodic regularity of temperature screening devices. Failure to get accurate temperature readings may result in over temperature conditions that are not only risky to safety, but also to product quality. Maintain documentations of the calibration and substitute broken temperature sensors at the right time.
Proper Material Handling Procedures
Safe handling of material eliminates jamming, fire hazard, and injury to operators. Always review compatibility of any materials before you feed them to the machine and ensure compatibilities on your operating temperatures and pressure. Other materials may emit hazardous fumes or may be ignited when heated.
Load feed materials making them straight and in the middle to avoid curling or bunching at the edges, which otherwise creates jams. Keep the right amount of tension during the procedure- little tension permits wrinkles and folds, and too much tension might wind up with the materials tearing or snapping out.
Never reach in when making changes or repositioning of materials in the rollers. Whenever carrying out any change, always use the normal shutdown procedures or the emergency stop button. Hands and loose clothing must be far away at nip points where materials get into the rollers.
In place clear procedures of dealing with material jams or feeding issues. Such practices ought to include deactivating machines, letting hot parts cool before touching and using the right tools instead of hands in order to clear jams.
Emergency Response Procedures
No matter how good you are at prevention, there may still be some emergencies. Random incidents have the potential of becoming catastrophic when there are no well-rehearsed emergency response procedures.
All the operators should be familiar with the emergency stop controls location and their procedure functioning. These are to be maintained and have to be tested on a regular basis and avoid obstructions. Along with the machine-mounted stops, you may also install some other emergency stops in strategic places around the bigger equipment.
Of special importance is the fire suppression procedure as the temperatures involved are quite high. Make proper fire extinguishers accessible at short distances and ensure the knowledge of operator on how to use them safely. Class A extinguishers are used to put out normal combustibles and Class C extinguishers are required to suppress electrical fire.
Establish particular tactics covering various disasters, such as fire, electrical failures, material backlogs of a critical nature and injury of the operators. Hang these procedures large next to every machine and practice drilling regularly so that every staff person is fully aware of his or her responsibilities.
Keep the current emergency contacts and make sure every operator is aware of how to request assistance in an accelerated manner. When there is more than one machine utilized in a facility, institute clear communication procedure that can be used in communicating when there is an emergency to other operators.
Regular Maintenance and Safety Checks
A major aspect of safety in heat transfer roller machine is preventive maintenance. Prepare extensive maintenance programmes that include all important safety items, including those that are not in relation to production.
Consistent care has to be given to the roller alignment and pressure settings. Calibration of the rollers leads to an unequal pressure performance and aggravates the chances of jammed materials or broken equipment. Make sure that roller pressure is set to factory recommendations and do not use excess pressures.
The moving parts are lubricated and this prevents the premature wear and the mechanical failure. Do not use non-suggested by manufacturer lubricants and apply lubrication as prescribed. Maintain comprehensive records of maintenance in order to monitor the state of equipment and detect possible issues before they turn into worries concerning safety.
The maintenance of electrical systems should only be undertaken by technicians. Nonetheless, the operators are to be trained to realize the symptoms of electrical issues, e.g., strange smells, sparks, or uneven functioning. Report such problems as soon as they appear, and put equipment out of action until repairs can be done.
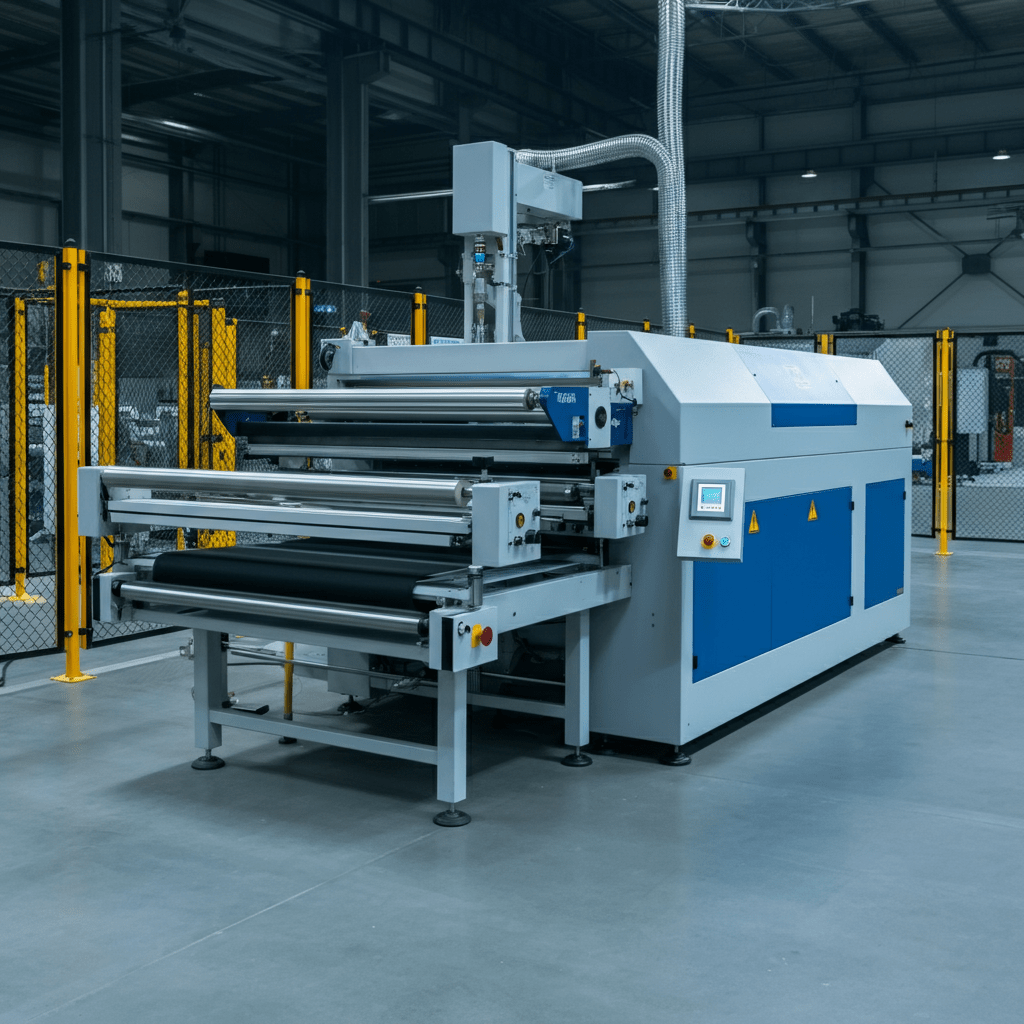
Training and Certification Requirements
The basis of any successful safety program is complete operator training. Any person operating, maintaining or working near or around heat transfer roller machines has to be trained accordingly before they start working.
The first training must include operation of equipment, safety techniques, emergency response, and personal protective equipment use. Such training has to be recorded and before the operator is allowed to work alone, he should show that he is competent.
Continuing safety training maintains safety awareness and deals with novel hazards or procedure changes. Regularly (every so often) contact refresher sessions and check-ups on safety should be scheduled to recheck crucial ideas, and share lessons learned during accidents or near-miss incidents.
One of the recommendations would be to have formal certification programs to the operators especially when it comes to more complicated or high-hazard pieces of equipment. Certification schemes maintain the standard of training and allow clear records to be made of the qualification of operators.
Creating a Culture of Safety Excellence
Doing whatever is required here as regards to ceremony is not the same as carrying these heat transfer roller machine safety considerations through to get a workplace where safety is appreciated, exercised and continually enhanced. All the best safety programs have powerful procedures, along with firm support of the leadership and involvement of the workers.
Safety audits and checks will regularly guide areas that are not satisfactory and may also direct that subsequent safety standards are met. Operation of operators should be encouraged to report near-misses and other safety issues that they may have without the fear of punishment. Such reports are likely to expose dangers even before they bring about accidents.
Also keep in mind that safety rules are not unmutable documents and need to be revised due to new equipments, materials or lessons learned. Have regular checks and reviews on your safety procedures and engage skilled operators on how to evaluate the quality of the safety procedures.
The cost of your investment in a complete safety training and work practices will reap you the amount you invested in a decrease in accidents and insurance rates, employee morale and continuous production. Above all, observing good heat transfer roller machine safety standards would guarantee that all operators go back home safely at the end of a given working day.